Gestione Controllo Spessori di Serbatoi per Stoccaggio Liquidi Pericolosi
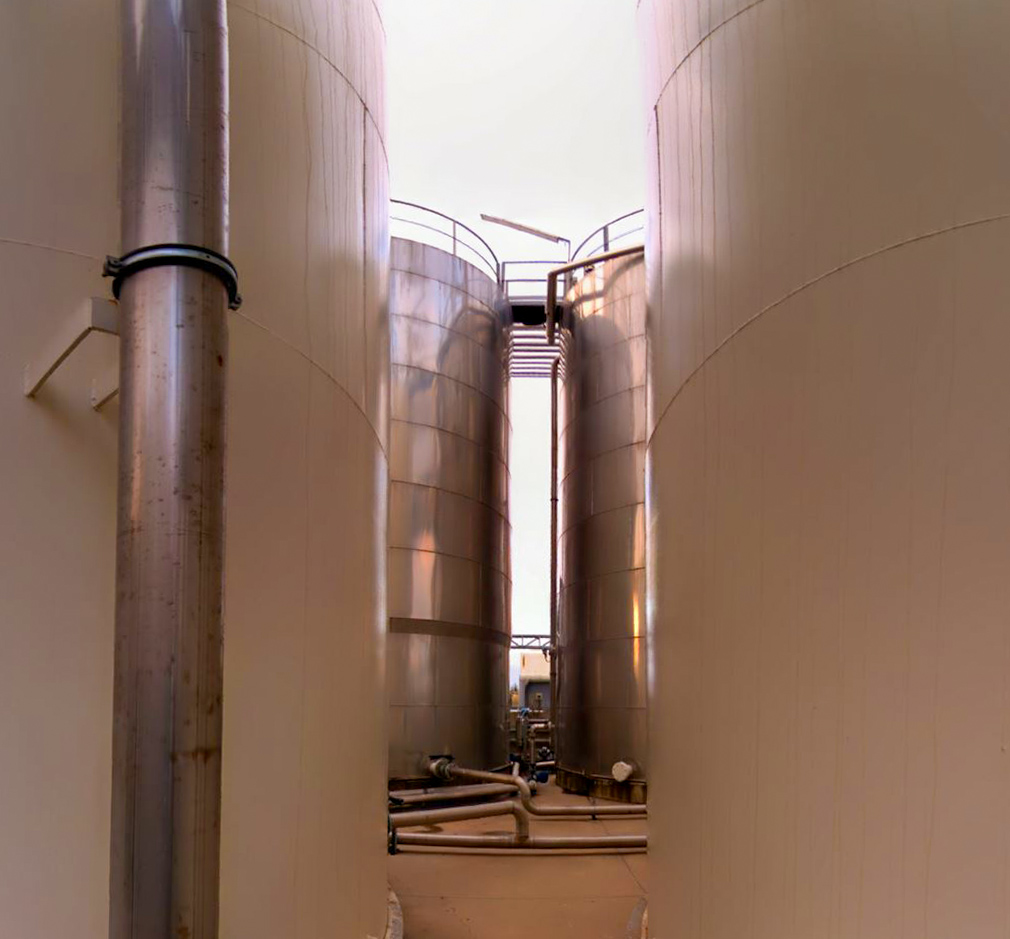
QUALE PUNTO DI PARTENZA?
Il cliente aveva necessità di implementare un sistema efficiente per i controlli periodici annuali sugli spessori dei serbatoi utilizzati per lo stoccaggio di liquidi pericolosi. Questi controlli sono fondamentali per monitorare lo stato di corrosione delle strutture e prevenire potenziali incidenti ambientali o di sicurezza.
L’intero processo doveva rispettare rigorosamente diverse normative tecniche: la UNI EN ISO 16809:2019 per la misurazione degli spessori mediante ultrasuoni, la ISO 9712 per la qualificazione degli operatori addetti alle prove, e la ISO 16809:2017 che regolamenta la strumentazione da utilizzare.
La mancata esecuzione di questi controlli secondo normativa esponeva il cliente a sanzioni e, in caso di incidenti con danni a persone o all’ambiente, al rischio che le polizze assicurative non coprissero i danni. Oltre agli aspetti normativi, emergevano esigenze implicite fondamentali: avere il controllo completo della documentazione, poter confrontare i report degli interventi passati con quelli nuovi, pianificare efficacemente gli interventi futuri, garantire la sicurezza dei dati e dell’impianto, ed evitare fermi di produzione ottimizzando l’efficienza delle operazioni.
QUALE SOLUZIONE?
La nostra soluzione si è sviluppata su due fronti paralleli: procedurale e tecnologico.
Sul fronte procedurale, abbiamo definito un protocollo rigoroso per garantire che le misure effettuate a distanza di anni fossero sempre confrontabili, assicurando l’accuratezza delle misurazioni nel tempo. Abbiamo inoltre standardizzato il formato dei report finali consegnati al cliente, garantendo la conformità alle normative e facilitando l’analisi comparativa dei dati. Questo ha richiesto lo sviluppo di competenze specialistiche all’interno del nostro team per effettuare controlli di alta precisione.
Sul fronte tecnologico, invece di adottare un approccio tradizionale basato su documentazione cartacea, abbiamo implementato una soluzione digitale integrata. Abbiamo utilizzato la piattaforma CDE (Common Data Environment) insieme all’applicazione DOCUMAINT®, creando un modello di fabbrica digitale completo.
Avendo già collaborato con il cliente su un progetto precedente, disponevamo della scansione 3D di parte dello stabilimento e dei modelli tridimensionali di alcuni serbatoi. Abbiamo quindi completato il modello digitale dell’intero stabilimento e caricato tutto sulla piattaforma di condivisione. Utilizzando la funzione “SmartObject” dell’app DOCUMAINT®, abbiamo creato i modelli dei serbatoi mancanti, integrando così l’intera infrastruttura nell’ambiente virtuale.
Successivamente, abbiamo caricato in formato digitale (PDF) i report dei controlli precedenti, collegandoli ai rispettivi serbatoi nella loro posizione reale all’interno dello stabilimento virtuale. Questo ha permesso di programmare gli interventi di controllo secondo le cadenze previste dalla normativa, con notifiche automatiche via email a tutti gli operatori e responsabili coinvolti.
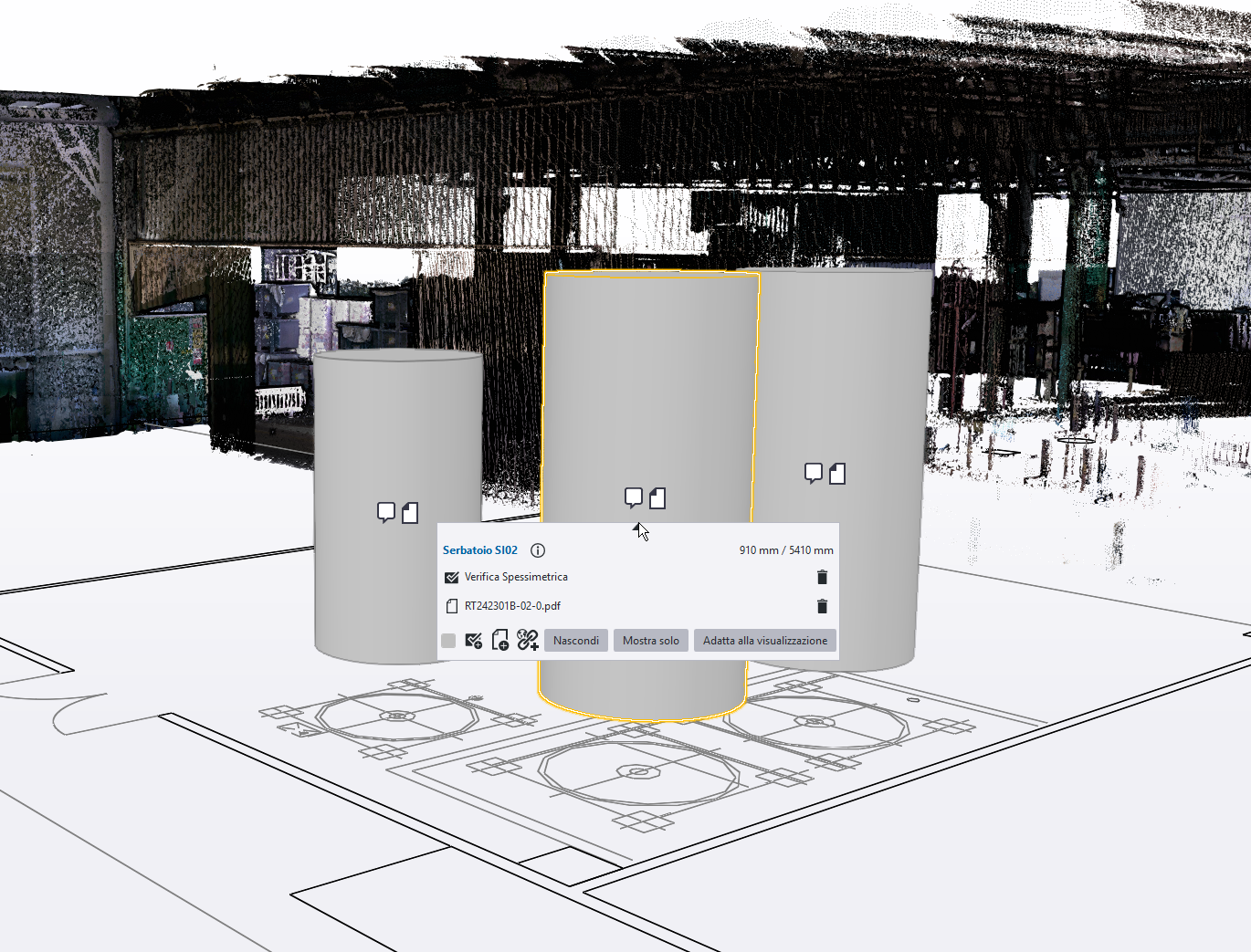
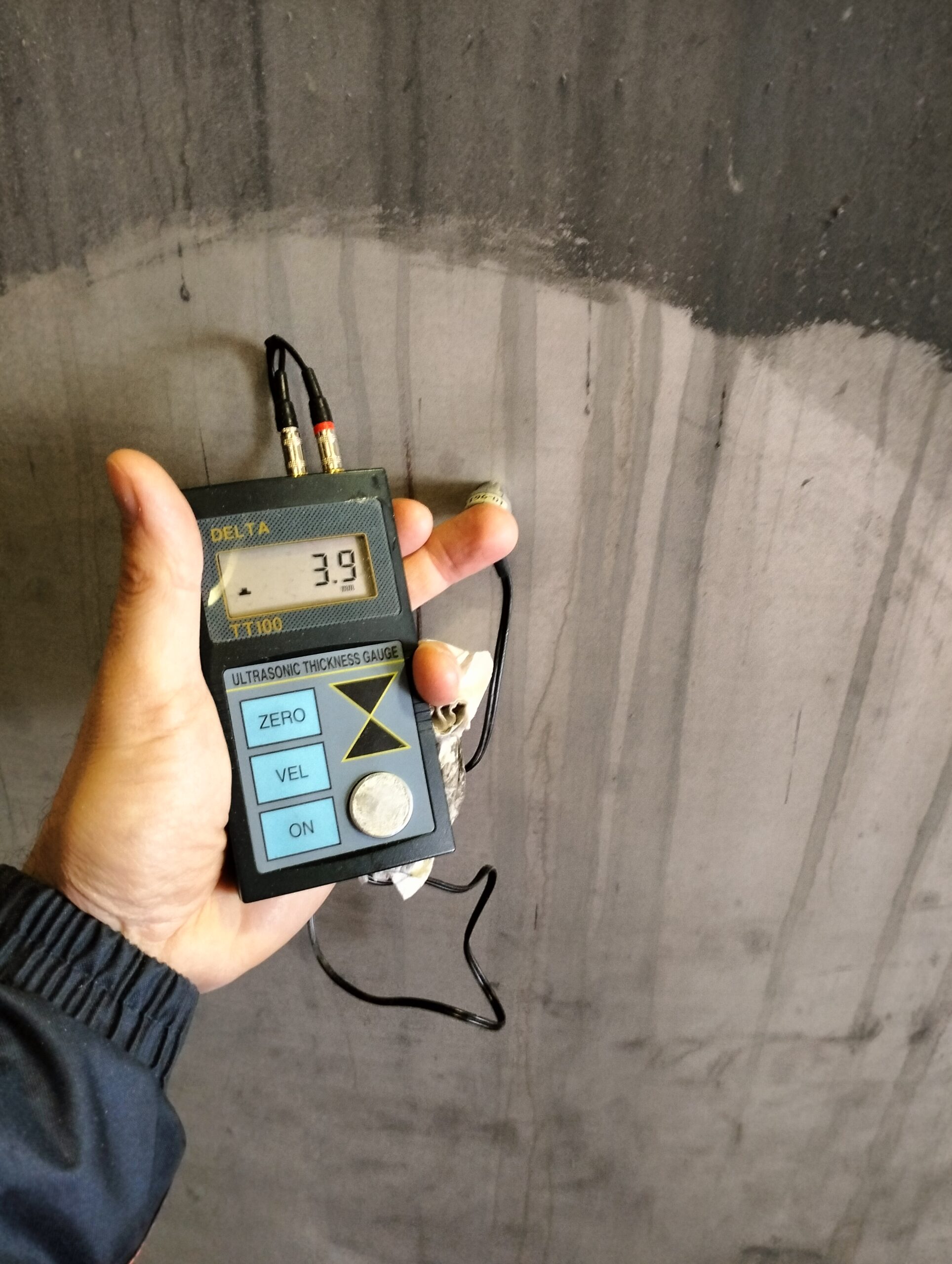
QUALE RISULTATO?
L’implementazione di questo sistema integrato ha generato benefici significativi e misurabili per il cliente.
Innanzitutto, abbiamo raggiunto l’obiettivo principale di garantire una condivisione e reperibilità immediata della documentazione, offrendo una visione realistica della correlazione tra i report e i serbatoi all’interno dello stabilimento. Il cliente può ora visualizzare in tempo reale lo stato di ogni serbatoio e accedere immediatamente alla documentazione relativa.
Il programma di controllo spessimetrico dei serbatoi è ora completamente digitalizzato e condiviso con tutti gli stakeholder, permettendo una pianificazione efficace e trasparente. Gli aggiornamenti avvengono in tempo reale, garantendo che tutti i soggetti coinvolti abbiano sempre accesso alle informazioni più recenti.
Un vantaggio particolarmente apprezzato dal cliente è la possibilità di creare link specifici per ogni serbatoio, utilizzabili in qualsiasi documento, che permettono di accedere direttamente al modello digitale corrispondente. Inoltre, per ciascun serbatoio è stato generato un QR Code che, una volta applicato fisicamente alla struttura, consente agli operatori sul campo di accedere istantaneamente al modello digitale e consultare tutta la documentazione collegata.
Questo sistema ha notevolmente migliorato la conformità normativa, ridotto i rischi operativi e ottimizzato l’efficienza delle ispezioni, evitando fermi non programmati dell’impianto.
QUALE TECNOLOGIA?
Il progetto si basa su un ecosistema tecnologico avanzato ma di facile utilizzo, composto da elementi complementari che lavorano in sinergia.
Il cuore del sistema è la piattaforma CDE (Common Data Environment), che funge da ambiente centralizzato per la condivisione e gestione di tutti i dati relativi ai serbatoi. Questa piattaforma consente una gestione strutturata delle informazioni, garantendo che tutti gli utenti autorizzati possano accedere ai dati rilevanti secondo i propri livelli di autorizzazione.
Complementare alla piattaforma CDE è l’applicazione DOCUMAINT, che rappresenta l’interfaccia operativa del sistema. Attraverso DOCUMAINT, abbiamo creato e gestito il modello di fabbrica digitale, utilizzando la funzione “SmartObject” per rappresentare virtualmente i serbatoi nella loro posizione reale all’interno dello stabilimento.
La tecnologia di scansione 3D è stata impiegata per creare una rappresentazione digitale fedele dell’ambiente fisico, mentre i sistemi di misurazione ad ultrasuoni conformi alla ISO 16809:2017 hanno garantito precisione e affidabilità nelle misurazioni degli spessori.
Questo ecosistema tecnologico integrato ha permesso di digitalizzare completamente un processo tradizionalmente basato su documenti cartacei, offrendo al cliente una soluzione moderna, efficiente e conforme alle normative più stringenti del settore.
