Progettazione impianto di trattamento rifiuti riciclabili
QUALE PUNTO DI PARTENZA?
Nel 2020 la società ECOREK Srl ha commissionato alla società OMAR Srl di Spresiano (TV) la realizzazione di un nuovo impianto CSS presso lo Stabilimento di Termini Imerese – Zona industriale (PA). OMAR Srl si è avvalsa del supporto di Power Engineering Srl per la progettazione del layout dell’impianto, per la progettazione esecutiva delle strutture di carpenteria, delle macchine e delle linee di aspirazione.
L’impianto è destinato al trattamento di rifiuti riciclabili; il materiale da selezionare e separare “multimateriale leggero” come imballaggi di alluminio, acciaio, plastiche di vario materiale e colore.
Il materiale viene ricevuto in balle pressolegate oppure in sacchetti sfusi, scaricato all’interno della zona di ricevimento e avviato al ciclo di lavorazione per poi essere selezionato e suddiviso, in modo automatico, attraverso vagli separatori, aspiratori e lettori ottici, e manualmente dagli operatori nelle varie postazioni di lavoro, secondo dimensione, materiale (PE / PET, ferro, alluminio) e colore. Una volta effettuata la suddivisione, il materiale è stoccato in appositi magazzini e successivamente pressato.
Questo impianto avrebbe dovuto, dal punto di vista tecnico:
- essere progettato per trattare 16-18 tonnellate di materiale ogni ora;
- essere progettato per dividere il materiale di diversa natura secondo dimensione, materiale e colore, con un peso specifico di 80-100 Kg/m3, sia in modo automatico attraverso l’utilizzo di macchine dotate di lettore ottico, che manuale attraverso operatori specializzati posizionati in postazioni di cernita dedicate;
- garantire un elevato grado di separazione dei materiali plastici attraverso l’uso di un sistema di aspirazione in grado di prelevare il materiale più leggero, differenziarlo ulteriormente e reimmetterlo nuovamente nel flusso di selezione e separazione;
- essere realizzato all’interno di un edificio di circa 4800 mq in pianta ed un’altezza di circa 8 metri, al cui interno erano presenti degli elementi vincolanti e non modificabili quali colonne, travi, grondaie, pozzetti ecc… Elementi che avrebbero potuto complicare la collocazione delle numerose macchine previste (circa 250) al suo interno considerando anche la presenza di un dislivello della pavimentazione non quantificabile con strumenti non professionali.
Una sfida davvero impegnativa.
QUALE SOLUZIONE?
Abbiamo iniziato cercando di risolvere punto per punto le criticità.
La dimensione notevole dell’impianto in termini di numero di macchine presenti, unito al vincolo sulla superficie disponibile rappresentato dal capannone esistente, ci ha spinti per prima cosa a effettuare la scansione 3D del capannone stesso in modo da identificare in modo preciso e puntuale tutte le varie deformazioni e ostacoli presenti al suo interno. Dopo aver eseguito la scansione, l’abbiamo importata e utilizzata per creare un modello 3D del capannone che riproducesse in maniera fedele la realtà e gli spazi disponibili.
Questo modello è poi risultato indispensabile da utilizzare all’interno del software dedicato allo studio e sviluppo del layout di impianto come riferimento per la creazione di un DIGITAL TWIN. Un impianto di dimensioni notevoli anche nel virtuale: una volta modellate tutte le macchine, le strutture di carpenteria e le tubazioni il progetto ha richiesto uno spazio di archiviazione pari a circa 70 Gb.
Fino al 2020, precedentemente all’introduzione del metodo di progettazione “LAMAPIM” risultava difficile gestire un progetto completo in un unico file, a causa dell’enorme quantità di dati in gioco non supportato dai computer utilizzati. Occorreva semplificare il file stesso o i blocchi di disegno inseriti, con perdita di particolari significativi. Era inoltre difficile identificare la posizione esatta di più macchine nello spazio dell’impianto e di conseguenza aggiungere accessori e collegamenti tra di esse, senza poter disporre di idonee workstation ad altissime prestazioni. Seguendo il metodo LAMAPIM, attraverso l’utilizzo di una piattaforma tipo C.D.E. (Common Data Environment), abbiamo consentito di visualizzare tutti gli elementi in modo agevole a tutti gli Stakeholder del progetto, anche a chi non disponeva di un’attrezzatura professionale per la gestione di file di grandi dimensioni.
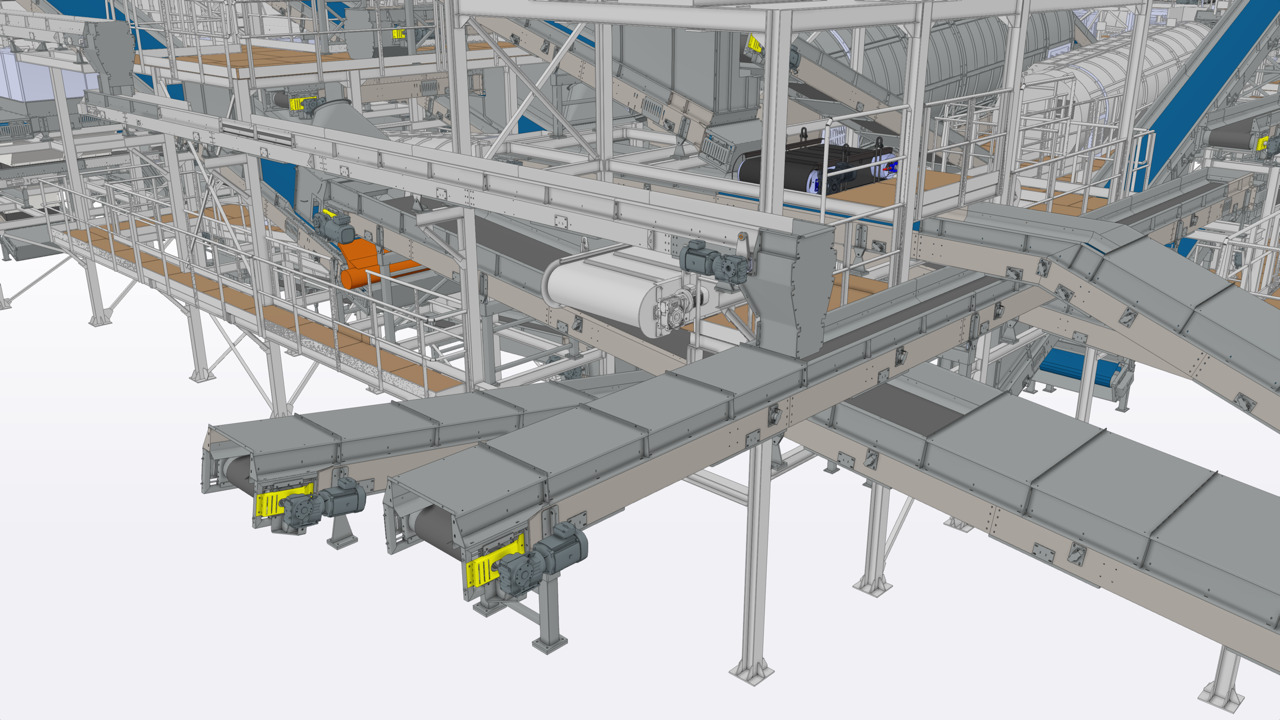
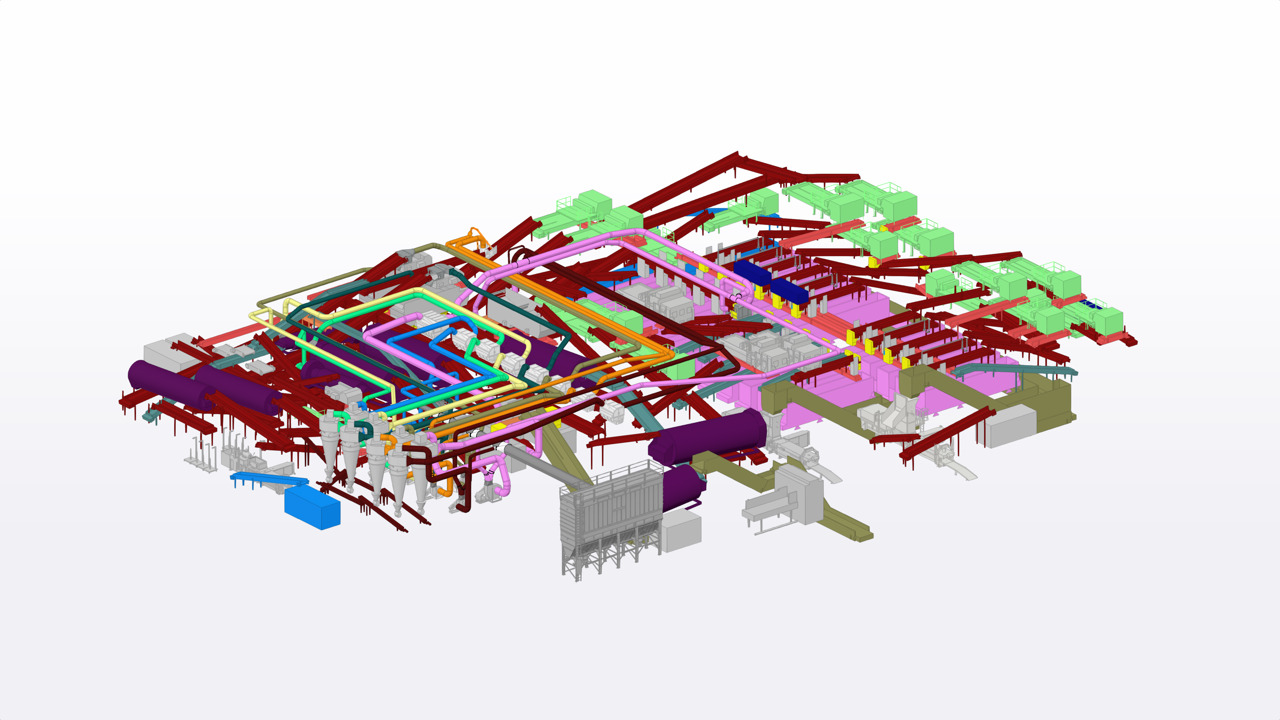
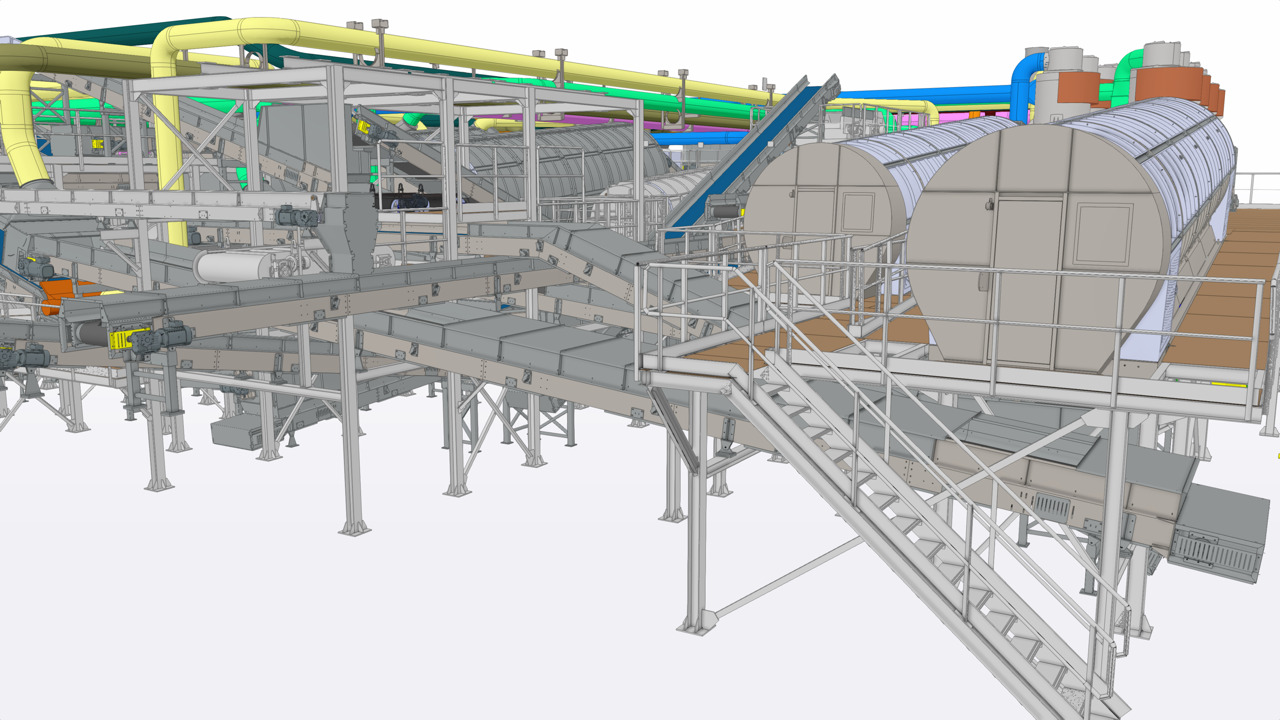
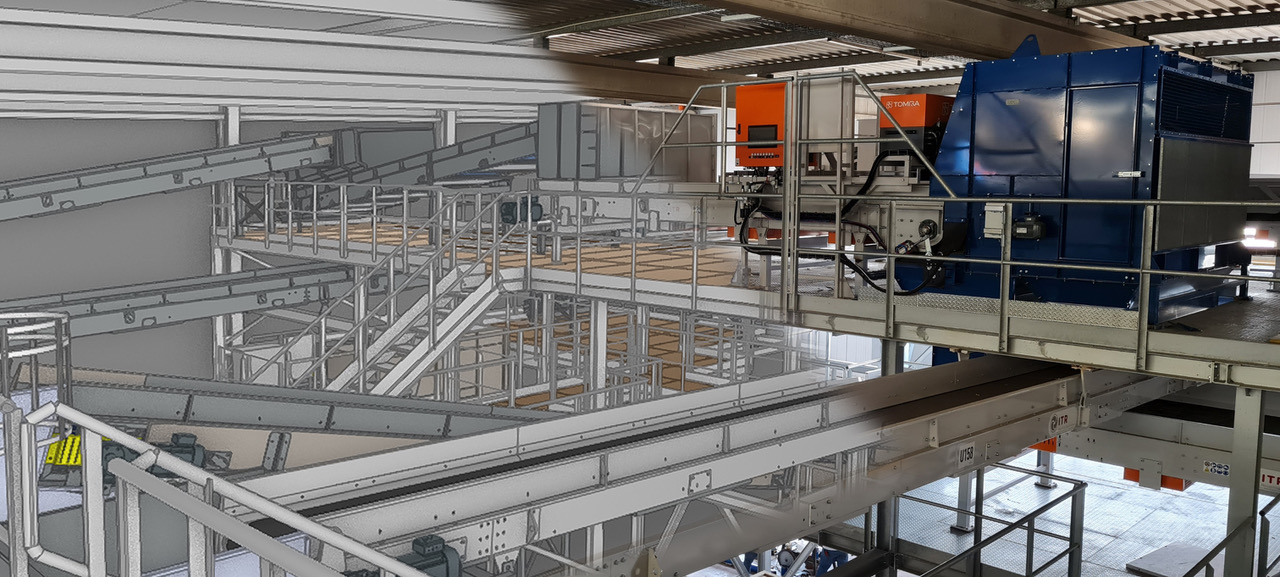
QUALE RISULTATO?
Delle circa 250 macchine previste in fase di progettazione, circa 200 sono state realizzate internamente dalla nostra azienda. Abbiamo investito in innovazione, utilizzando tecnologie all’avanguardia, con un’attenzione particolare al tema sicurezza.
I restanti 50 macchinari sono stati costruiti in collaborazione con fornitori o acquistati direttamente dal cliente, sotto la nostra supervisione.
QUALE TECNOLOGIA?
Ci siamo trovati ad affrontare un lavoro molto impegnativo in termini di gestione dati e files. Per questo motivo abbiamo deciso di sviluppare un nuovo approccio alla progettazione dei macchinari facendo interagire i vari software tramite un C.D.E. secondo un flusso di lavoro progettuale ben preciso, questo è LAMAPIM.
Questo strumento ci ha permesso di:
- comunicare e visualizzare in tempo reale tutti gli aggiornamenti apportati al layout in modo da individuare e modificare eventuali errori ed interferenze;
- integrare nel layout il 3D costruttivo delle singole macchine/strutture anche se progettate con l’ausilio di software CAD differenti;
- sviluppare in modo razionale i vari accessori meccanici di collegamento tra le varie macchine necessari al loro funzionamento;
- suddividere l’impianto in zone/aree, semplificando anche la fase di montaggio.
Risultato? Risparmio di tempo e taglio dei costi di realizzazione. Oltre a rispettare tutti i parametri imposti dal cliente siamo riusciti a progettare il layout di un impianto che riesce a selezionare il multimateriale al 95%, un successo che solo pochi impianti della stessa categoria hanno raggiunto. Durante la fase di montaggio abbiamo inoltre implementato un nuovo metodo di posizionamento e installazione: il C.D.E., con la sua visualizzazione 3D nello spazio virtuale, ha permesso di limitare l’utilizzo delle tavole di disegno per identificare la collocazione esatta di ogni macchina e limitare gli aggiustamenti dovuti a interferenze non previste tra le macchine e la struttura.
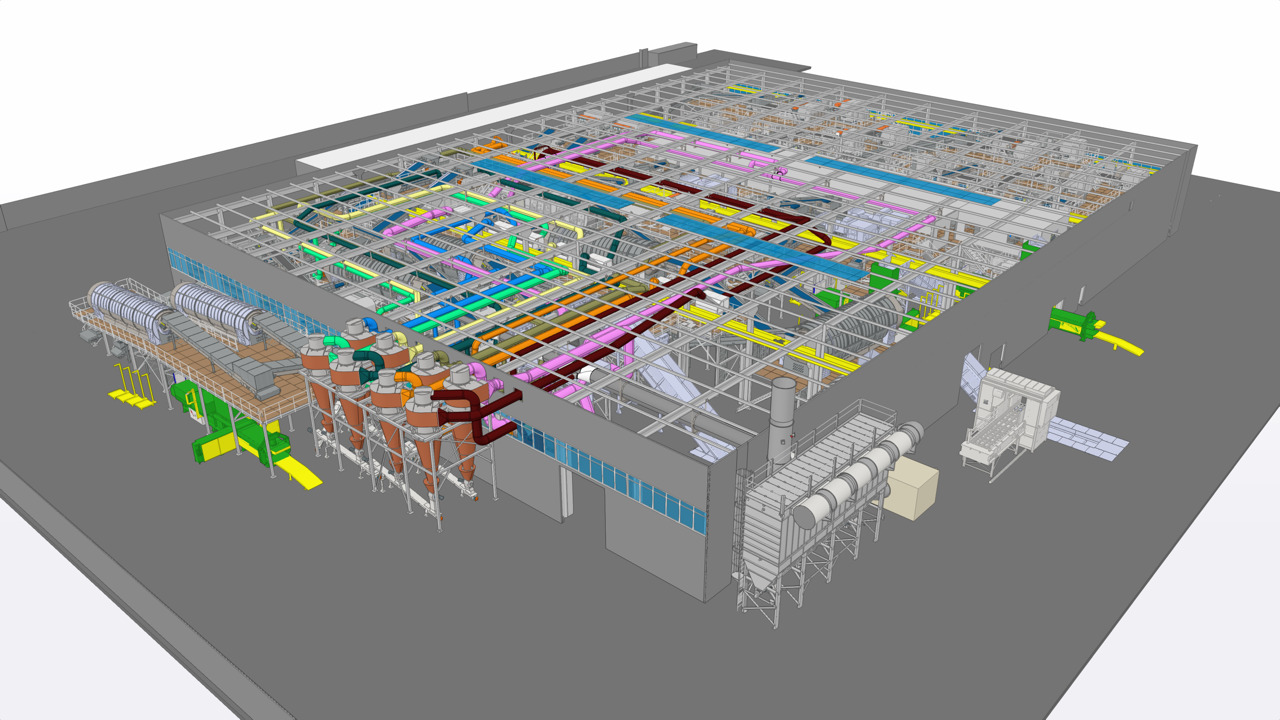