DESIGN OF RECYCLABLE WASTE TREATMENT PLANT
WHERE DID WE BEGIN?
In 2020 ECOREK Srl commissioned OMAR Srl a company located in Spresiano (TV)a new CSS plant at Termini Imerese Industrial Zone (PA). OMAR Srl sought the support of Power Engineering Srl for the plant layout design, detailed structural engineering, machinery and sucting line design.
The plant is intended for the treatment of recyclable waste, specifically the separation and sorting of “light multimaterial” such as aluminum packaging, steel, various plastics in different colors.
The material arrives in compacted bales or loose bags, is unloaded within the receiving area, and then processed through an automatic workflow involving separator screens, aspirators, optical readers, and manual sorting by specialized operators at various workstations, based on size, material (PE/PET, iron, aluminum), and color. Once sorted, the material is stored in specific warehouses and subsequently compacted.
From a technical perspective, this plant was intended to:
- process 16-18 tons of material per hour;
- separate different types of materials by size, material, and color with a specific weight of 80-100 Kg/m3, both automatically through optical reader-equipped machines and manually by specialized operators at sorting stations;
- ensure a high degree of separation of plastic materials using an suction system to extract lighter materials, then differentiate them, and reintroduce them into the sorting and separation process.
- be housed within a building of approximately 4800 square meters in floor area and a height of around 8 meters. The building contained fixed elements, such as columns, beams, gutters, and pits, which could have complicated the placement of numerous machinery (approximately 250) inside, considering an uneven floor level that couldn’t be accurately measured without professional tools.
A truly demanding challenge.
WHAT HAS BEEN THE SOLUTION?
We began by simplifying point by point each criticality.
The substantial size of the plant in terms of the amount of machinery, coupled with the constraint of the available space represented by the existing warehouse, led us to perform a 3D scan of the warehouse itself. This allowed us to precisely identify all deformations and obstacles within it. After the scan, we imported it and used it to create a 3D model of the warehouse that faithfully reproduced the actual conditions and available space.
This model proved essential to be used in a software dedicated to plant layout design as a reference to create a DIGITAL TWIN. The virtual plant was also substantial: once all machinery, structural elements, and pipelines were modeled, the project required approximately 70 GB of storage.
Untill 2020, prior introduction of the “LAMAPIM” design method managing a complete project in a single file was hard due to the enormous amount of data involved, which exceeded the capacity of the computers in use. Files or inserted drawings needed to be simplified, resulting in the loss of significant details. It was also difficult to precisely position multiple machines within the plant space and, consequently, tough to add accessories and connections between them without access to high-performance workstations. Using the LAMAPIM method and using a dataroom C.D.E. (Common Data Environment), we made it possible for all project stakeholders, even those lacking professional equipment to handle large files, to easily visualize all elements..
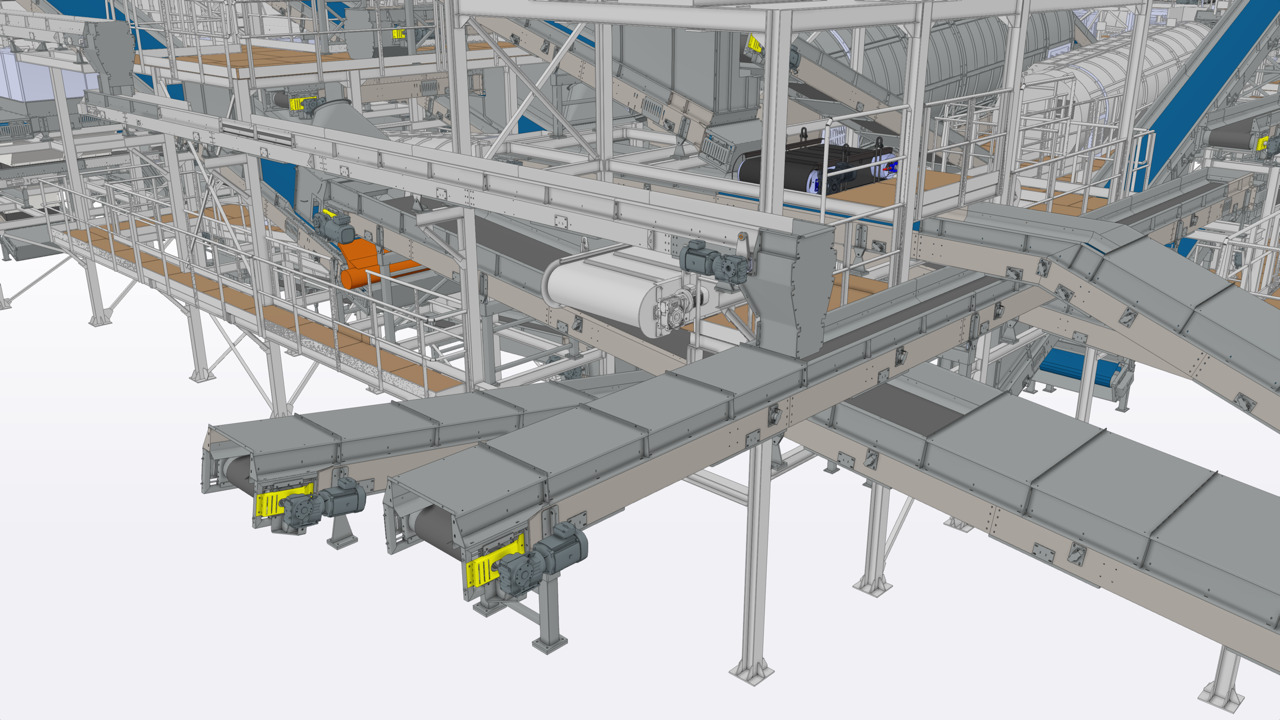
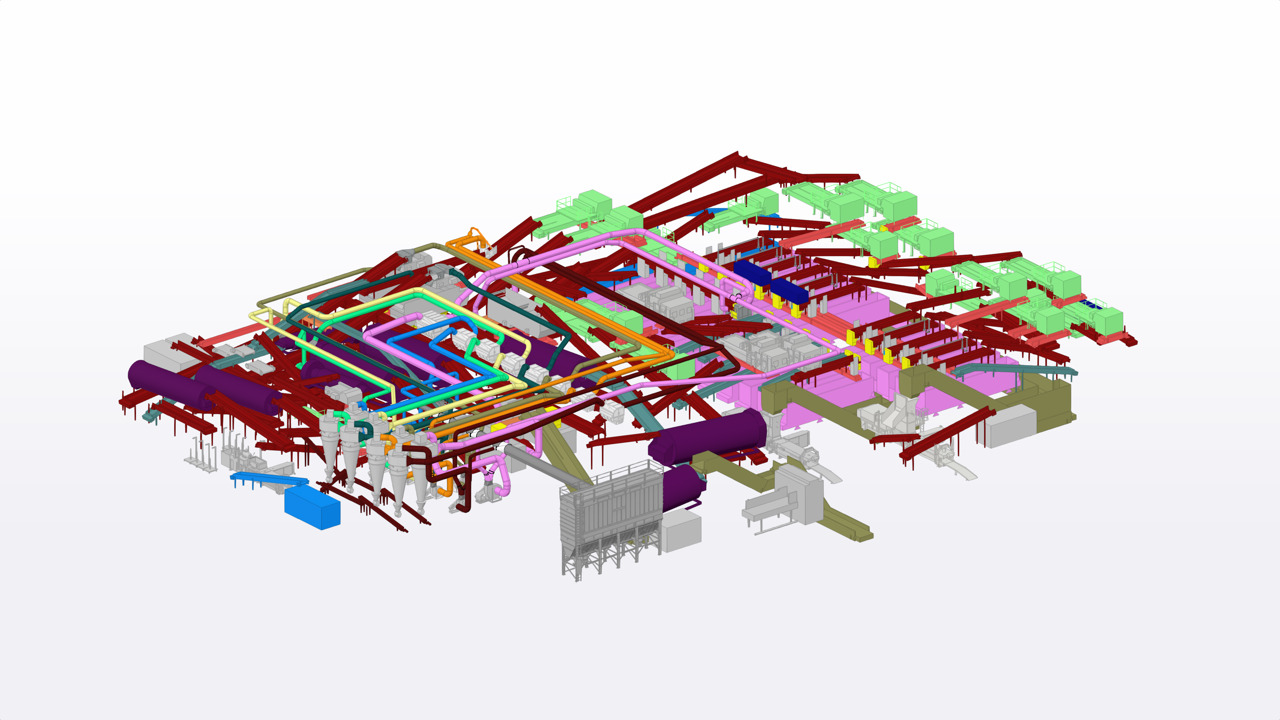
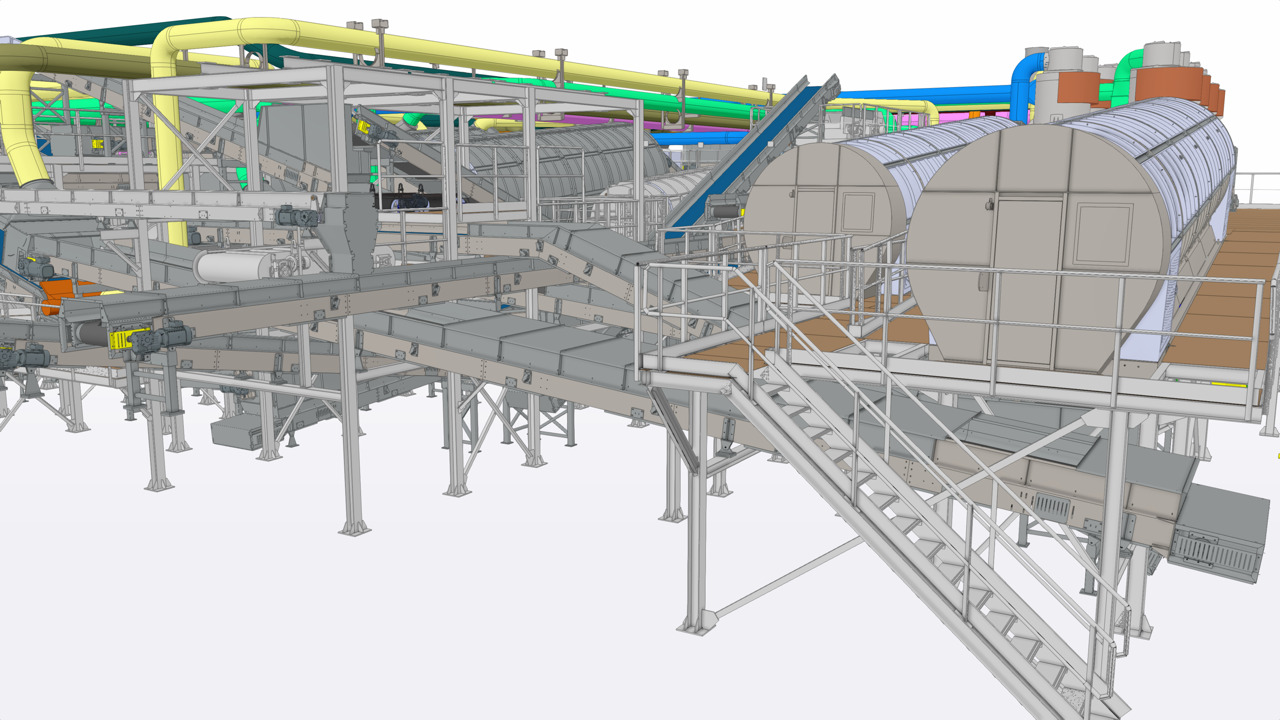
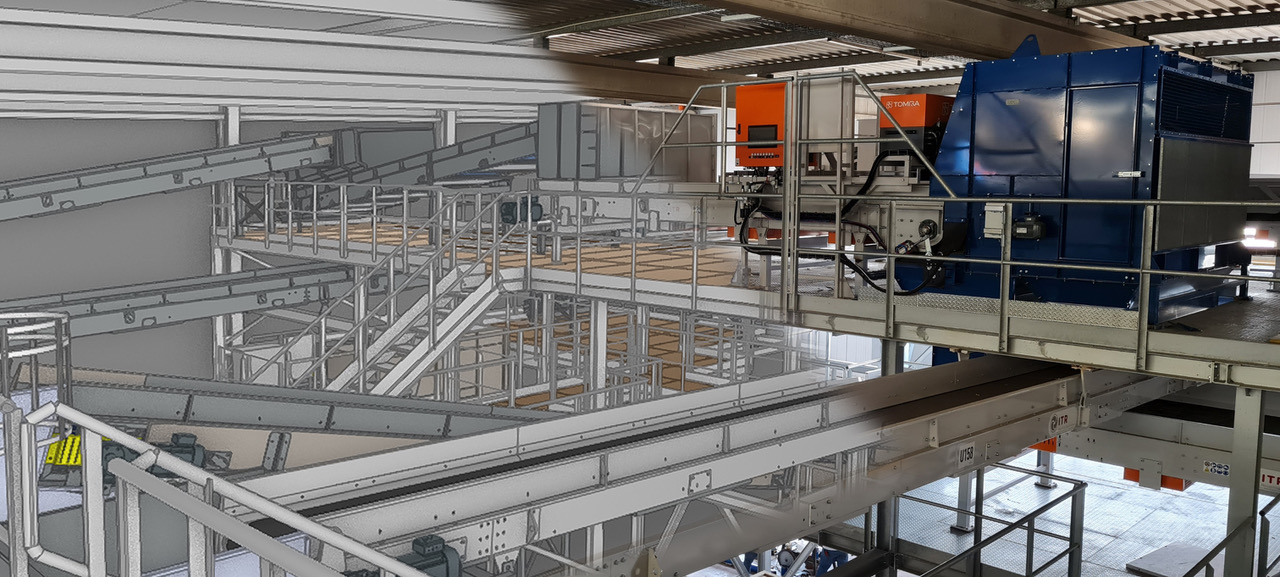
WHAT HAS BEEN THE OUTCOME?
Of the approximately 250 machinery planned during the design phase, about 200 were internally realized by our company. We invested in innovation, using cutting-edge technologies with a particular focus on safety.
The remaining 50 machines were either built in collaboration with suppliers or directly purchased by the client under our supervision.
WHAT TECNOLOGY ARE WE USING?
We found ourselves facing a very demanding task in terms of data and file management. For this reason, we decided to develop a new approach to machinery design by integrating various software through a CDE according to a well-defined design workflow, this is LAMAPIM.
This tool has allowed us to:
- communicate and visualize in real-time all updates made to the layout in order to identify and modify any errors and interferences;
- integrate the constructive 3D of individual machinery/structures into the layout even if designed using different CAD software;
- rationally develop various mechanical accessories to connect the various machinery necessary to operate;
- divide the plant into zones/areas, simplifying the assembly phase.
The result? Time savings and a reduction in costs. Not only we complied all parameters set by the client, we also managed to design the layout of a plant that can select multimaterial at 95%, a success achieved by only a few plants in the same category. During the assembly phase, we also implemented a new method of positioning and installation: the CDE, with its 3D visualization in virtual space, allowed limiting the use of drawings to identify the exact location of each machine and reduce adjustments due to unforeseen interferences between machines and the structure.
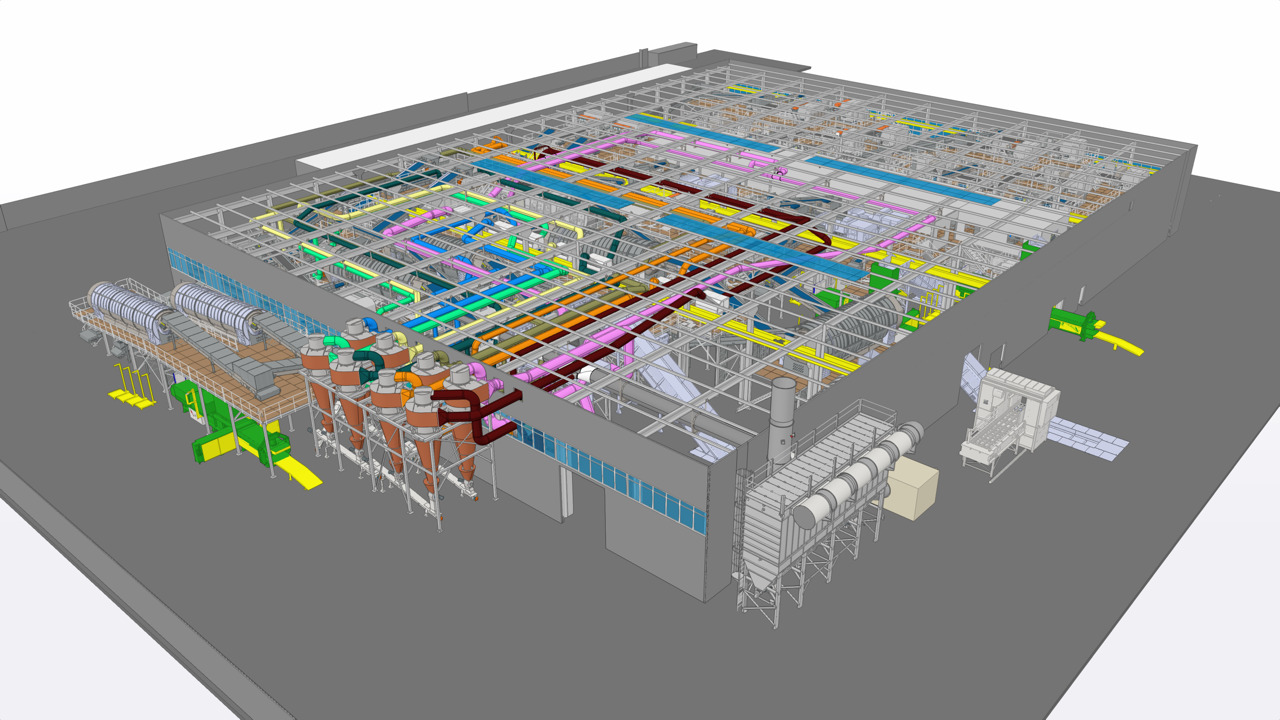