Transition from Paper-BASED Maintenance Management to Digital Factory
WHERE DID WE START FROM?
The client was facing a challenge common to many modern industries: improving the process of managing and reviewing documentation related to production line maintenance.
In an increasingly complex production environment, the traditional paper-based documentation system was showing obvious limitations in terms of efficiency, accessibility and updating.
The primary need concerned two fundamental aspects of document management: keeping documentation up-to-date following maintenance work and being able to retrieve it quickly in case of operational or control needs. This seemingly simple requirement concealed significant complexity, considering the volume of documents and frequency of maintenance work in a modern industrial plant.
In addition to the explicit requirements, there were several implicit needs of great strategic importance: to have complete control over documentation, to systematically monitor and update maintenance interventions, to avoid unplanned plant shutdowns by optimizing operational efficiency, and to ensure overall plant safety.
A particularly important need was the ability to decentralize maintenance management, overcoming dependence on a single professional figure and allowing multiple people to be involved in the process.
WHAT HAS BEEN THE SOLUTION?
Faced with these complex requirements, we chose to abandon the traditional paper-based approach to implement an integrated digital solution, using the Common Data Environment (CDE) platform in combination with the DOCUMAINT® application.
The first step of our intervention took advantage of a previous collaboration with the client: we already had the 3D scan of the plant, the actual state, the design and the complete floor plan of the facility. Starting from this base, we proceeded to enrich the existing digital model by adding specific elements of the production line.
Using the DOCUMAINT® app and in particular the “SmartObject” function, we created an accurate digital representation of a machine from the production line and workshop, respecting its actual dimensions and location within the plant. This operation allowed us to complete the digital factory model, an essential precondition for the effective use of the DOCUMAINT® system.
Next, we collected all the documentation regarding the machine, digitized it and uploaded it within the CDE platform through the DOCUMAINT® application. In this way, each digitized document was linked to the corresponding machine at its actual location within the digital model of the plant.
Finally, we configured the system to schedule maintenance work according to the maintenance plan provided by the customer. The DOCUMAINT® app was set up to automatically send email alerts to all control operators and managers whenever a new intervention is created. With each completed maintenance intervention, the system allows the digitized documentation to be updated with a new version through the platform.
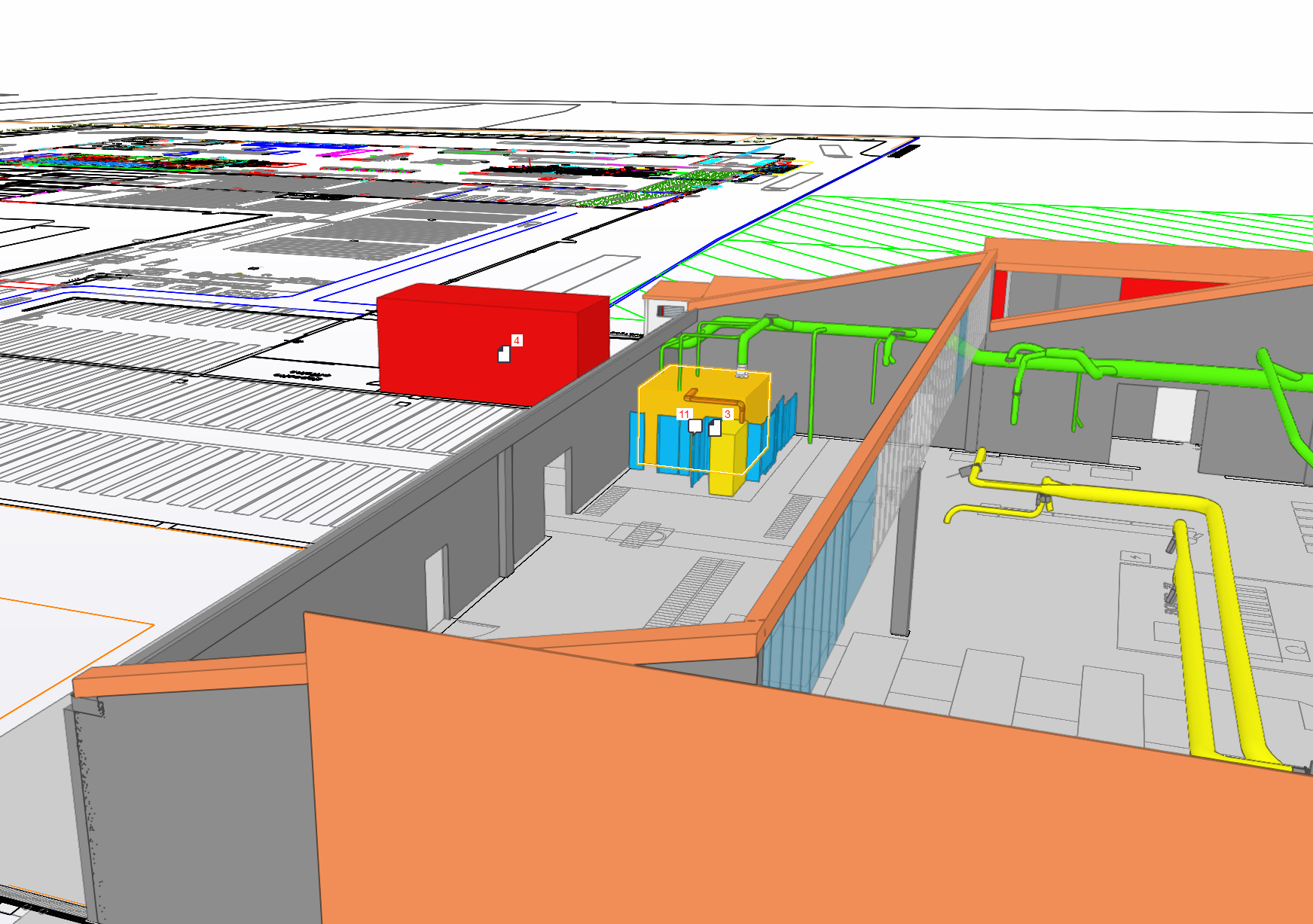
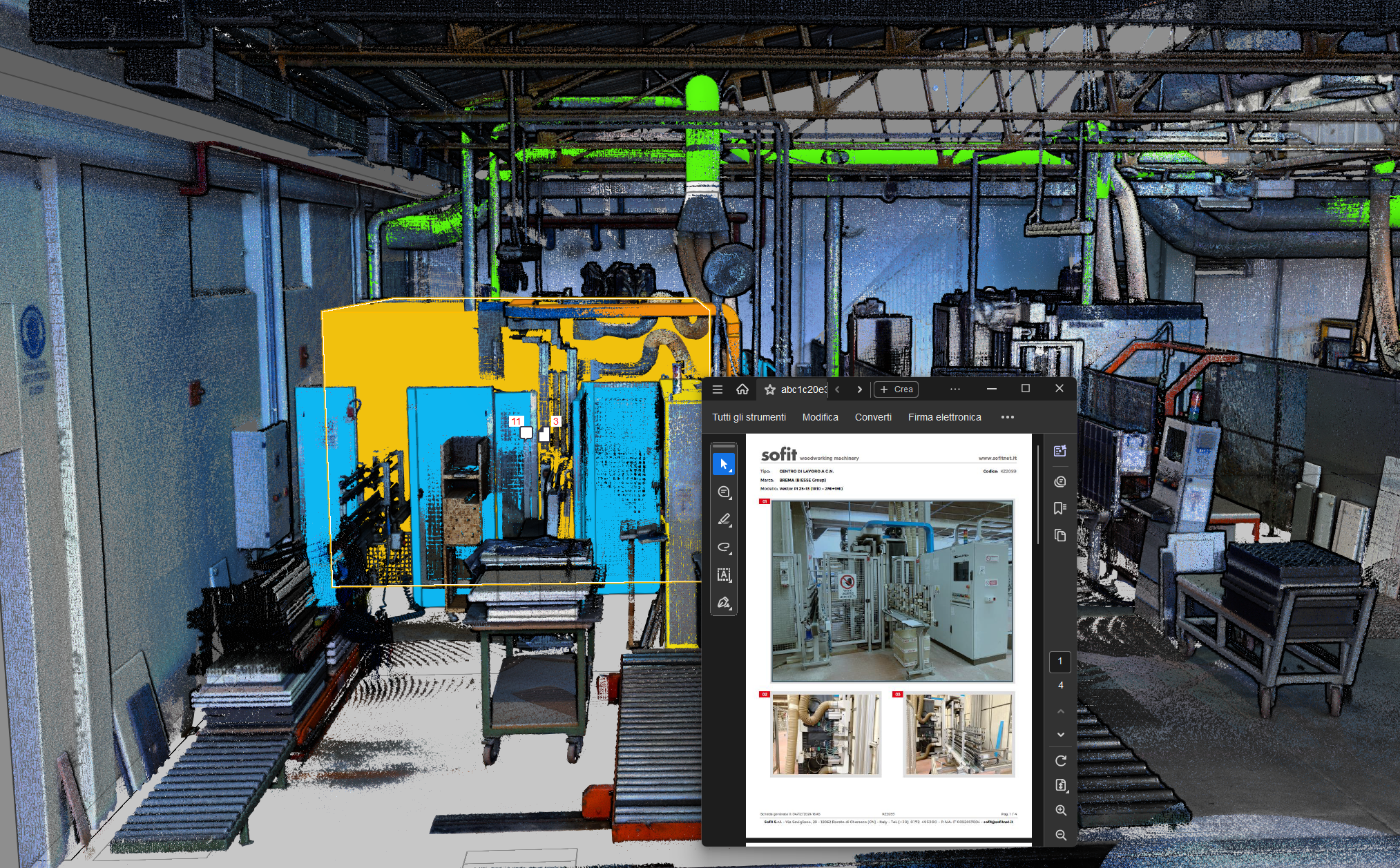
WHAT HAS BEEN THE OUTCOME?
The transition from paper-based to digital management has generated tangible and immediate results for the customer, radically transforming the maintenance process.
The first and most obvious benefit has been the immediate sharing and findability of documentation, which is always updated in real time. Operators and managers now have access to a realistic view that clearly highlights the correlation between each document and the related machine within the plant.
The production line maintenance program became a shared tool, accessible to all authorized users within the project. This has made it possible to overcome the previous centralization of knowledge, distributing responsibilities and skills among multiple professionals and reducing organizational vulnerability.
Access to documentation is now quick and easy, allowing necessary documents to be viewed at any time, even during unscheduled interventions or emergency situations. This immediacy results in reduced intervention time and greater overall operational efficiency.
A particularly appreciated feature is the ability to create, for each machine, specific links that can be used in any file, allowing the customer to directly access the corresponding digital model. In addition, a QR Code can be generated for each machine that can be physically applied to the equipment, making it easier for operators in the field to directly access the digital model and consult the associated documentation.
WHAT TECNOLOGY ARE WE USING?
The project is based on an integrated technology ecosystem, consisting of complementary elements working in synergy to provide a comprehensive and user-friendly solution.
3D scanning technology was used in the initial phase to create a faithful digital representation of the plant’s physical environment. This technology allows the dimensions and geometric features of spaces and structures to be captured with a high level of accuracy, creating the basis for the digital factory model.
The Common Data Environment (CDE) platform is the centralized environment for managing and sharing all maintenance-related data. This platform enables structured information management, ensuring that all authorized users can access relevant data according to their authorization levels.
The DOCUMAINT® application forms the operational interface of the system, through which we created and managed the digital factory model. DOCUMAINT®‘s “SmartObject” function was particularly important for virtually representing the machines in their actual location within the factory and linking relevant documentation to each of them.
The QR Code generation system completes the technological ecosystem, creating a bridge between the physical and digital environments. These codes, physically applied to machines, allow operators to instantly access digital documentation by simply scanning the code with a mobile device.
This combination of technologies has created an integrated system that overcomes the limitations of traditional paper-based management, offering a modern, efficient and scalable solution for industrial maintenance management.
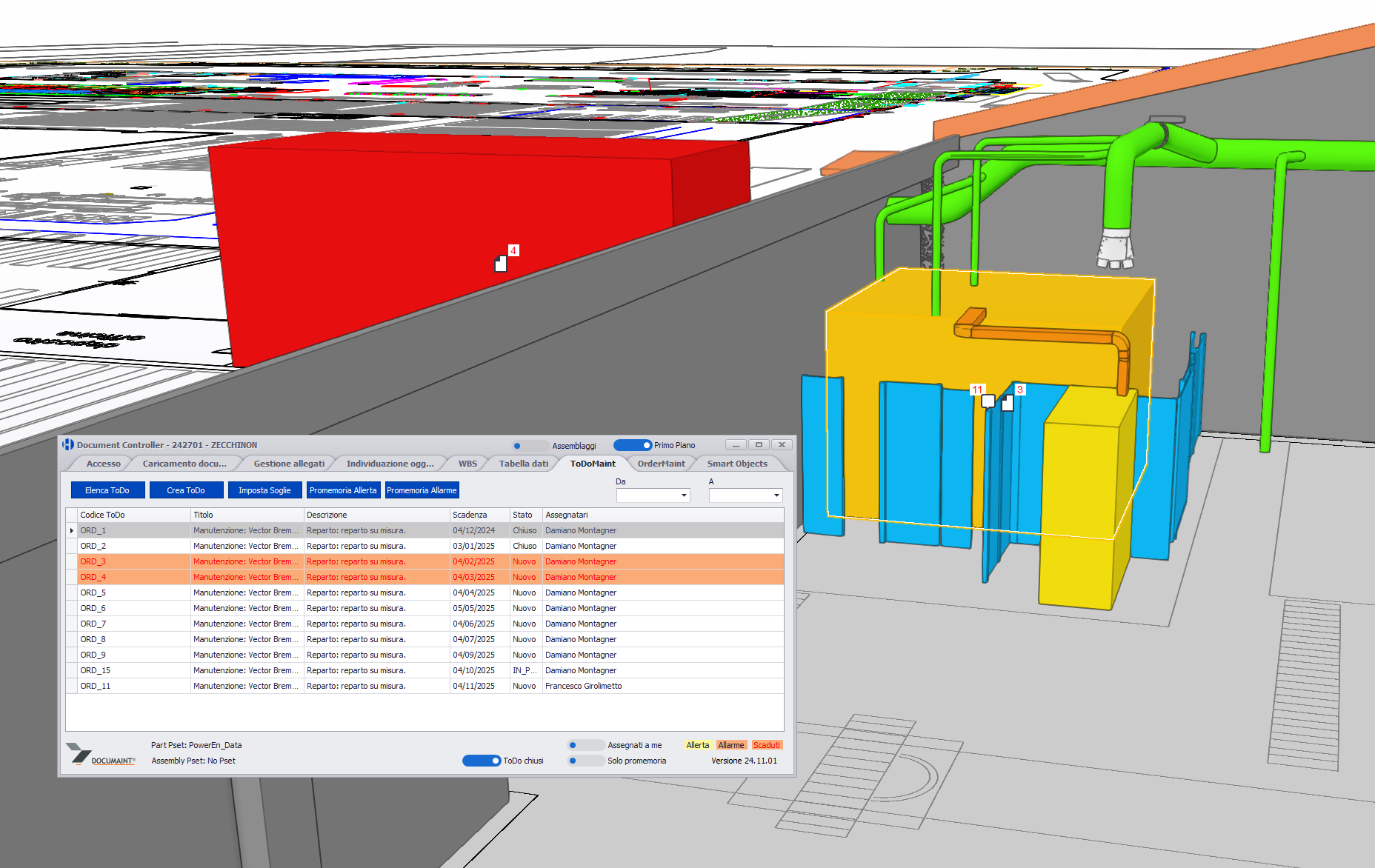