Fire Prevention Documentation Management System
WHERE DID WE START FROM?
The client needed an effective system to manage documentation related to the facility’s fire protection system. The main need was to be able to quickly share documentation regarding fire extinguishers and safety devices during customer audits. Specifically, in addition to simple archiving, it was critical to be able to access, update, and retrieve these documents quickly.
The documentation to be managed included fire system diagrams, certifications and tests, inspection reports, operation and maintenance manuals, emergency plans, and personnel training documentation. All of this had to comply with UNI 9994-1:2024, which regulates the initial inspection and maintenance of fire extinguishers.
Implicitly, the client also required to simplify the documentation management and search process, have full control over the documents, and monitor and schedule audits, thus ensuring optimal management during audits.
WHAT HAS BEEN THE SOLUTION?
To meet the client’s needs, we implemented an integrated system based on the Common Data Environment (CDE) platform and DOCUMAINT application. Our solution was developed through several strategic steps.
At first, we took advantage of the 3D scan of the plant already in our possession from previous collaborations with the same client. This allowed us to pinpoint the exact location of all fire prevention devices within the building without the need for additional surveys.
Next, using the DOCUMAINT app and the “SmartObject” feature, we created simplified 3D models to mark the location of each fire extinguisher within the digital factory. We then collected, digitized, and uploaded all documentation related to the fire prevention devices to the CDE platform.
Using this approach, each digitized file is now linked to the relevant fire extinguisher and virtually positioned in its actual location within the plant. The system also allows control interventions to be scheduled according to the cadence established by the regulations: all assigned operators and customer managers automatically receive email alerts for scheduled interventions.
With each revision, the documentation is updated in real time on the platform, ensuring that the information is always current and immediately accessible.
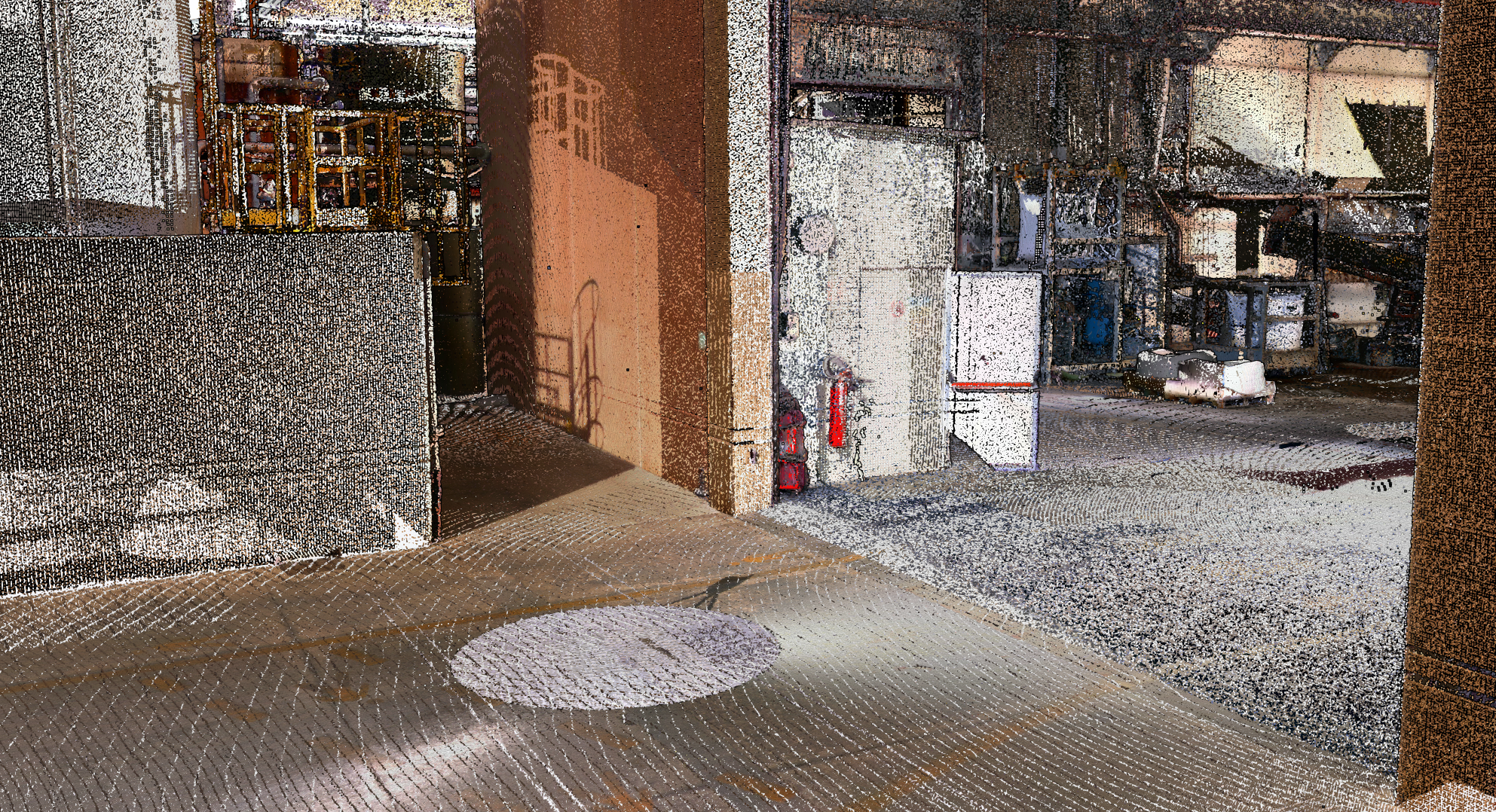
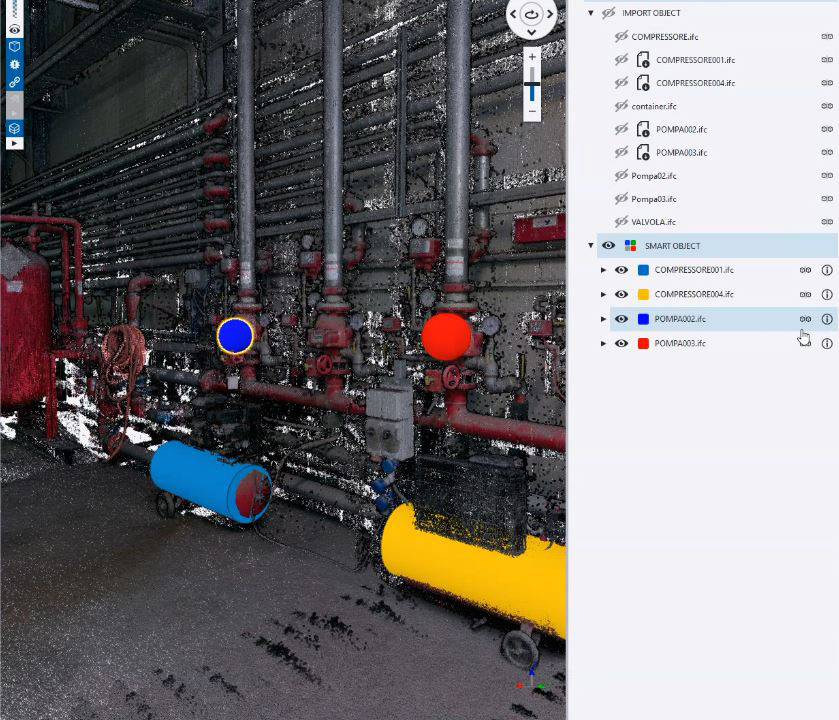
WHAT HAS BEEN THE OUTCOME?
The implementation of the system has led to significant results for the client. First, we have achieved immediate sharing and retrieval of documentation, which is always updated in real time. The system provides a realistic view of the correlation between document and fire prevention devices within the fire system, allowing quick and easy access to view documents at any time.
An important added value is the ability to create, for each fire prevention devices, links that can be used in any file, allowing the customer to access the digital model directly. In addition, a QR Code can be generated for each fire prevention devices that can be physically attached to the device, making it easier for field operators to immediately access the digital model and view associated documentation.
This approach has greatly improved the efficiency of the document management process, reducing search and update times, and ensuring greater reliability during customer audits. Automated maintenance scheduling has also optimized resource management and ensured compliance with current regulations.
WHAT TECNOLOGY ARE WE USING?
The implemented solution is essentially based on two complementary technologies:
- The Common Data Environment (CDE) platform constitutes the central environment for data management and sharing. This platform acts as a unified repository for all documents related to the fire system, allowing their structured organization and controlled access.
- The DOCUMAINT app represents the operational interface of the system. Thanks this app, we were able to create the digital factory model, using the “SmartObject” function to virtually represent the fire prevention devices in their actual location. DOCUMAINT also allows us to schedule and monitor periodic maintenance work, send automatic notifications, and update documentation in real time.
- The integration of these technologies with 3D scanning of the plant has enabled the creation of a faithful digital representation of the plant, where each fire extinguisher is linked to its own documentation and easily identifiable, both virtually and physically through QR Codes.
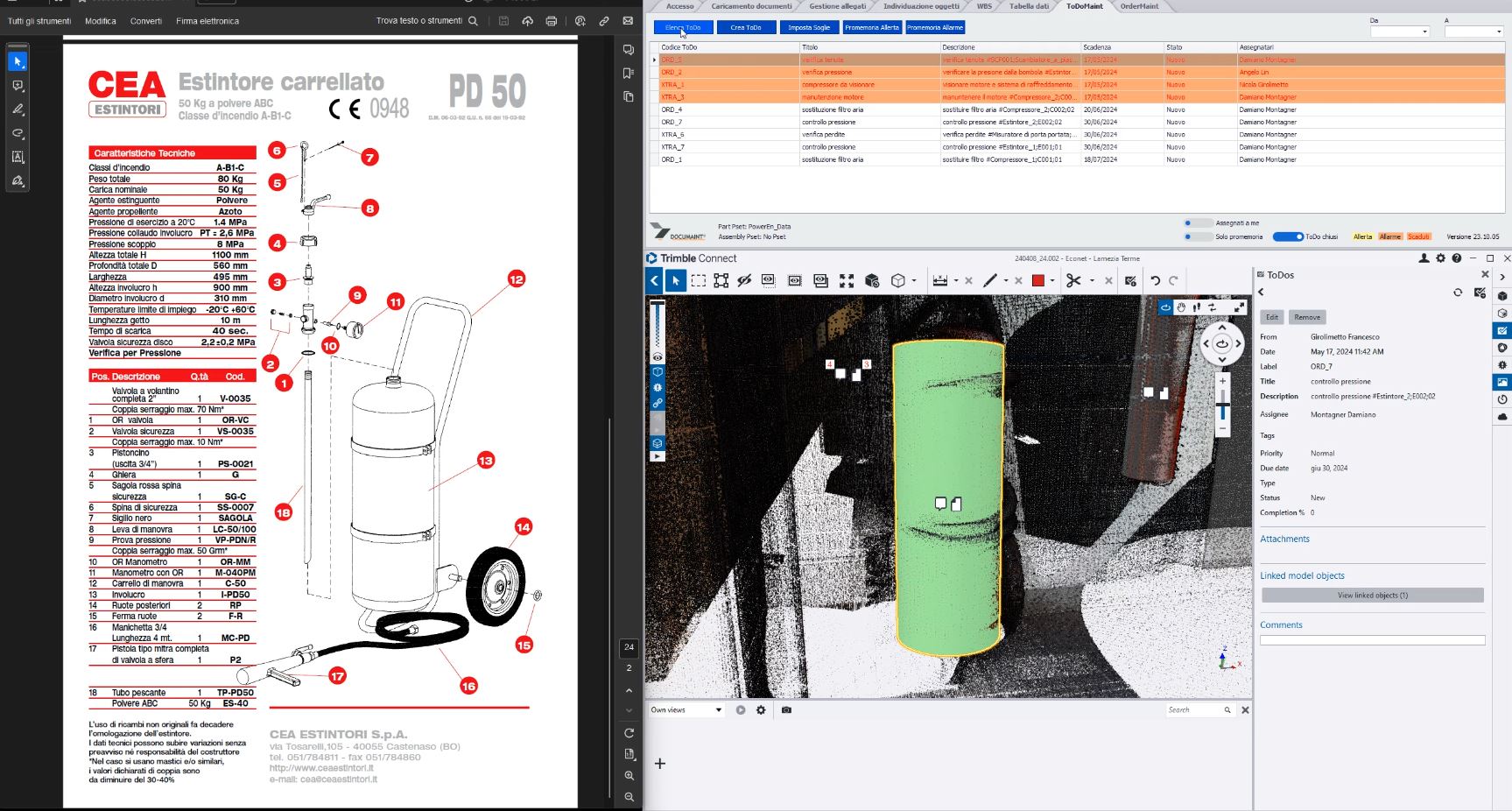