Thickness Control Management of Hazardous Liquid Storage Tanks
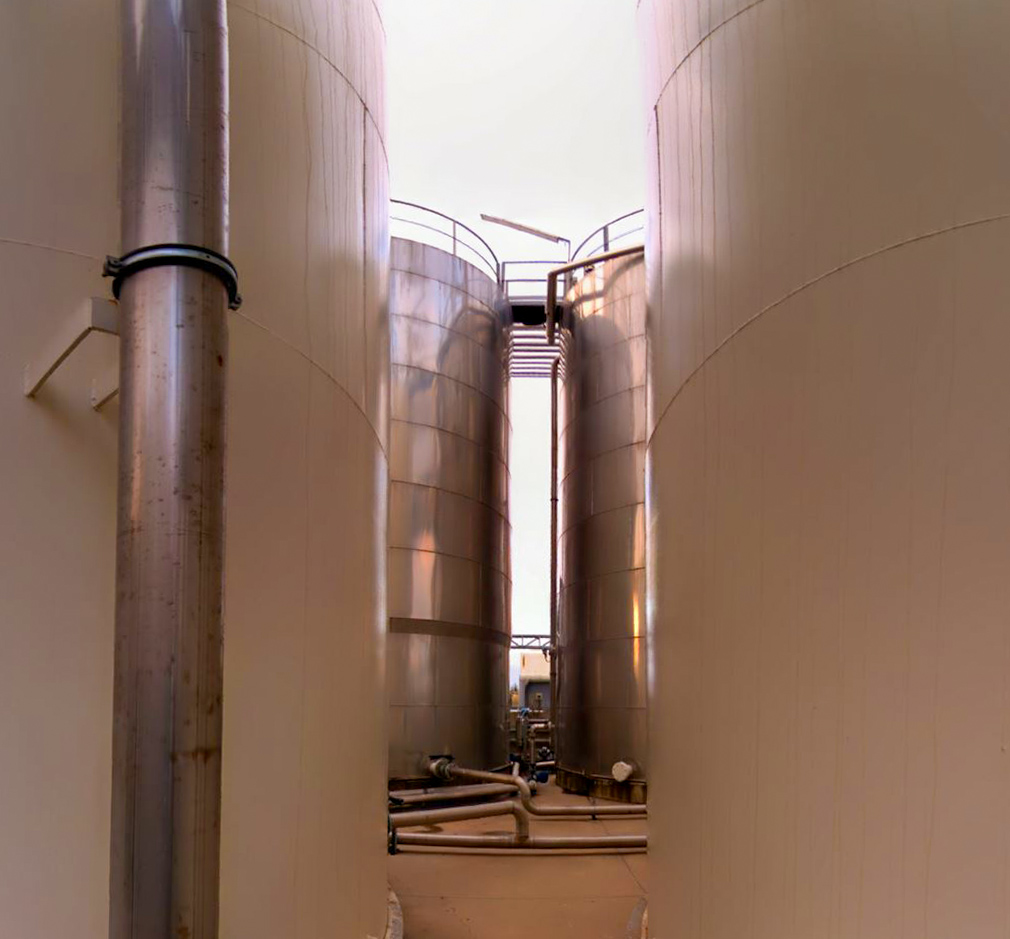
WHERE DID WE START FROM?
The client needed to implement an efficient system for annual periodic checks on the thicknesses of tanks used for storing hazardous liquids. These checks are essential to monitor the corrosion status of the structures and prevent potential environmental or safety incidents.
The entire process had to strictly adhere to several technical standards: UNI EN ISO 16809:2019 for measuring thicknesses using ultrasound, ISO 9712 for the qualification of test operators, and ISO 16809:2017, which regulates the instrumentation to be used.
Failure to perform these checks according to regulations exposed the client to penalties and, in the case of accidents with personal or environmental damage, the risk that insurance policies would not cover the damage. In addition to the regulatory aspects, fundamental implicit needs emerged: to have complete control of documentation, to be able to compare reports of past interventions with new ones, to effectively plan future interventions, to ensure data and plant security, and to avoid production stoppages by optimizing the efficiency of operations.
WHAT HAS BEEN THE SOLUTION?
Our solution was developed on two parallel fronts: procedural and technological.
On the procedural front, we defined a strict protocol to ensure that measurements taken years apart were always comparable, ensuring the accuracy of measurements over time. We also standardized the format of the final reports delivered to the client, ensuring regulatory compliance and facilitating comparative data analysis. This required the development of specialized skills within our team to perform high-precision checks.
On the technology front, instead of taking a traditional paper-based approach, we implemented an integrated digital solution. We used the CDE (Common Data Environment) platform together with the DOCUMAINT® application, creating a complete digital factory model.
Having already worked with the client on a previous project, we had 3D scans of part of the plant and 3D models of some of the tanks. We then completed the digital model of the entire plant and uploaded everything to the sharing platform. Using the “SmartObject” function of the DOCUMAINT® app, we created models of the missing tanks, thus integrating the entire infrastructure into the virtual environment.
Next, we digitally uploaded (PDF) reports of previous inspections, linking them to the respective tanks at their actual location within the virtual facility. This made it possible to schedule control interventions according to the cadences required by the regulations, with automatic email notifications to all operators and managers involved.
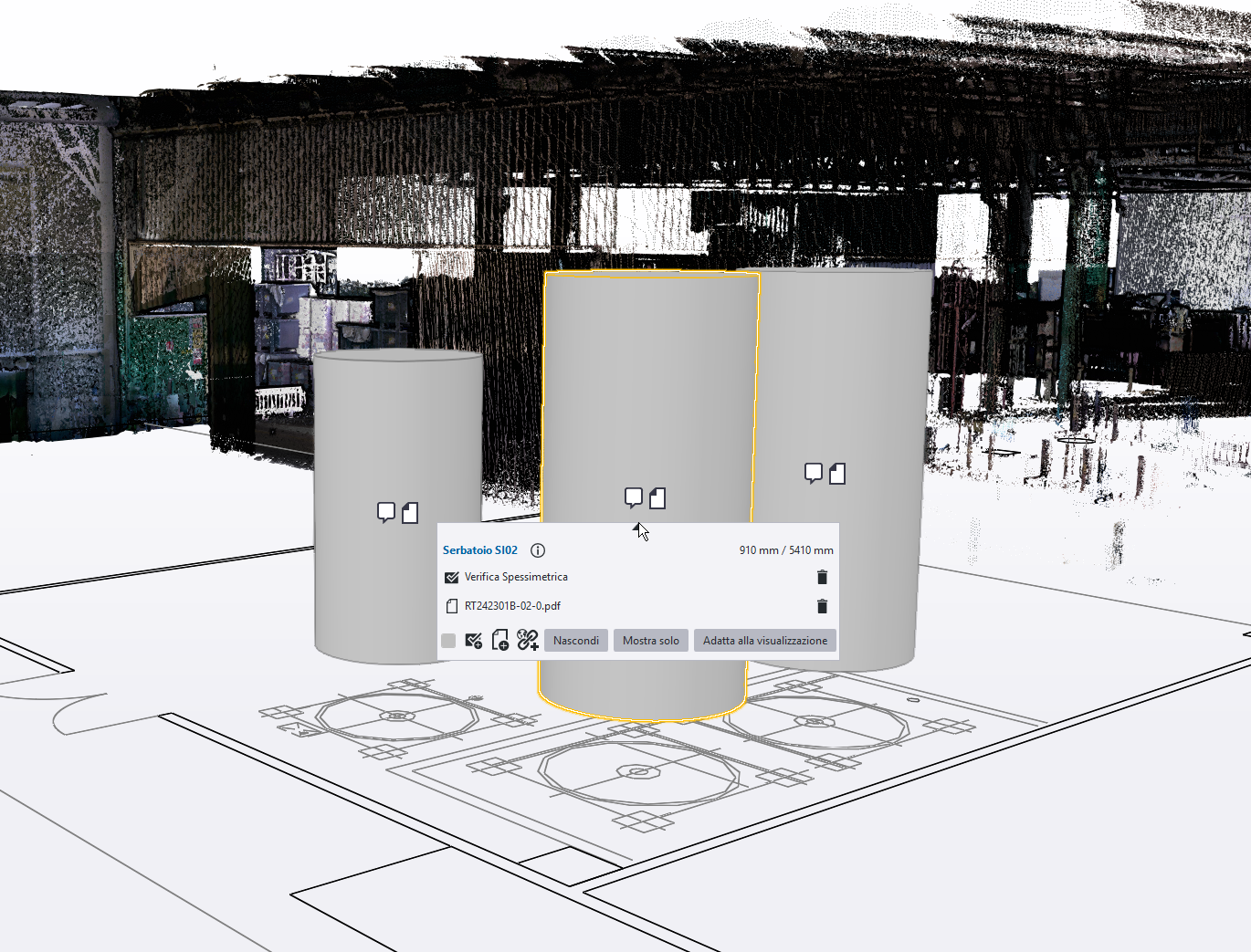
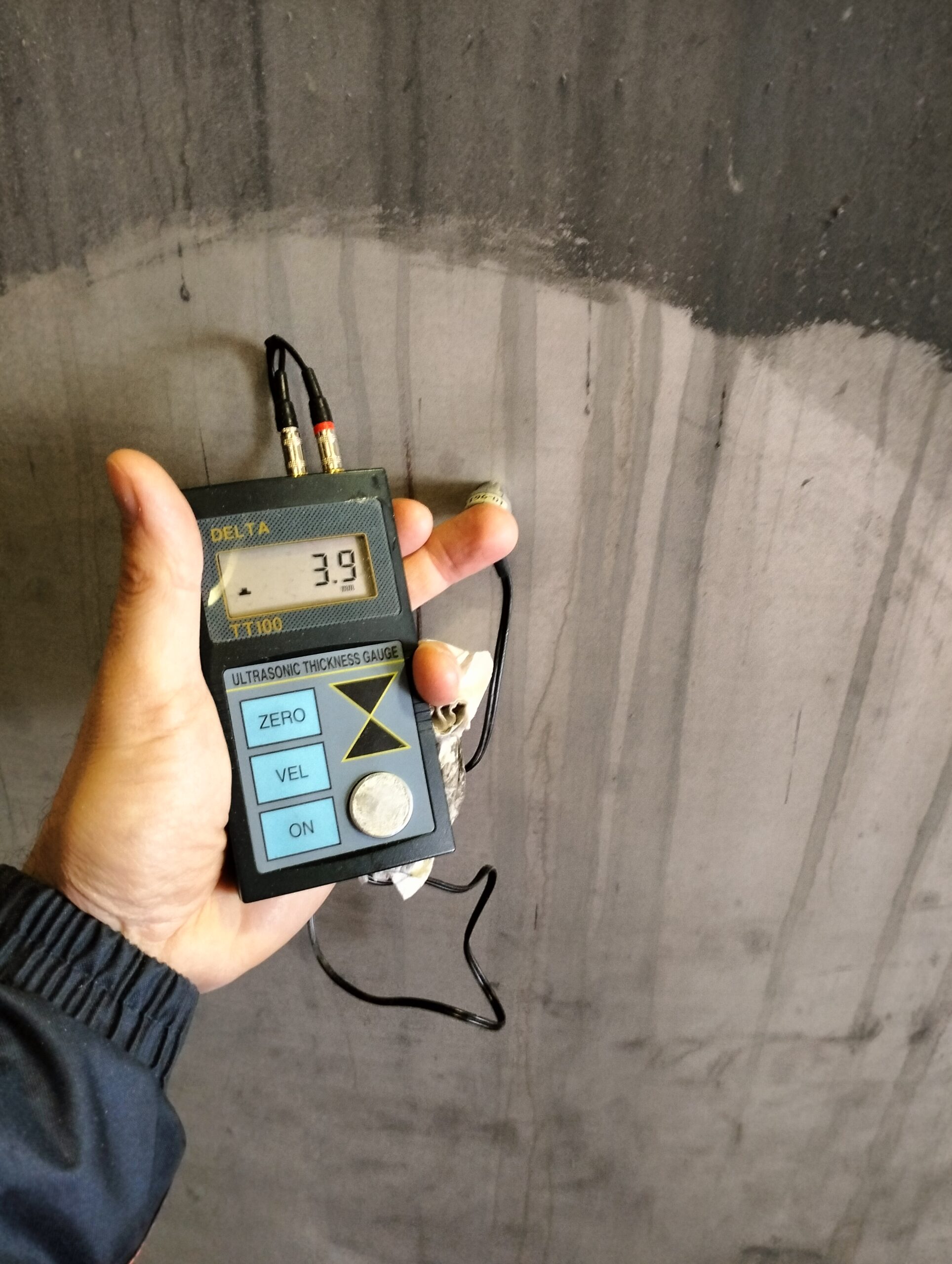
WHAT HAS BEEN THE OUTCOME?
The implementation of this integrated system has generated significant and measurable benefits for the client.
First, we have achieved the main objective of ensuring immediate sharing and retrieval of documentation, providing a realistic view of the correlation between reports and tanks within the plant. The customer can now view the status of each tank in real time and immediately access related documentation.
The tank thickness control program is now fully digitized and shared with all stakeholders, enabling effective and transparent planning. Updates occur in real time, ensuring that all stakeholders always have access to the latest information.
An advantage particularly appreciated by the client is the ability to create specific links for each tank, which can be used in any document, providing direct access to the corresponding digital model. In addition, a QR Code was generated for each tank that, once physically applied to the structure, allows field operators to instantly access the digital model and consult all related documentation.
This system has greatly improved regulatory compliance, reduced operational risks and optimized inspection efficiency by avoiding unplanned plant shutdowns.
WHAT TECNOLOGY ARE WE USING?
The project is based on an advanced yet user-friendly technological ecosystem composed of complementary elements that work in synergy.
At the heart of the system is the Common Data Environment (CDE) platform, which serves as a centralized environment for sharing and managing all reservoir data. This platform enables structured information management, ensuring that all authorized users can access relevant data according to their authorization levels.
Complementary to the CDE platform is the DOCUMAINT® application, which is the operational interface of the system. Through DOCUMAINT®, we created and managed the digital factory model, using the “SmartObject” function to virtually represent the tanks in their actual location within the plant.
3D scanning technology was used to create a faithful digital representation of the physical environment, while ISO 16809:2017-compliant ultrasonic measurement systems ensured accuracy and reliability in thickness measurements.
This integrated technology ecosystem enabled a traditionally paper-based process to be fully digitized, providing the client with a modern, efficient solution that complies with the industry’s most stringent regulations.
